ASSET CONDITION MONITORING
Reduce and prevent downtime. Make first-time fixes every time. Provide better assistance and strengthen customer loyalty. Remote monitoring and predictive maintenance for service is the best way to transform your business.
Implementing an IoT platform
Industrial companies face pressing challenges that require IIoT
solutions. From remote monitoring and service to workforce
efficiency and asset optimization, IIoT solves common challenges
across different industries
Digital Manufacturing
- Real-time Production Performance Monitoring
- Asset Monitoring & Utilization
- Connected Work Cell
- Digital and Augmented Work instruction
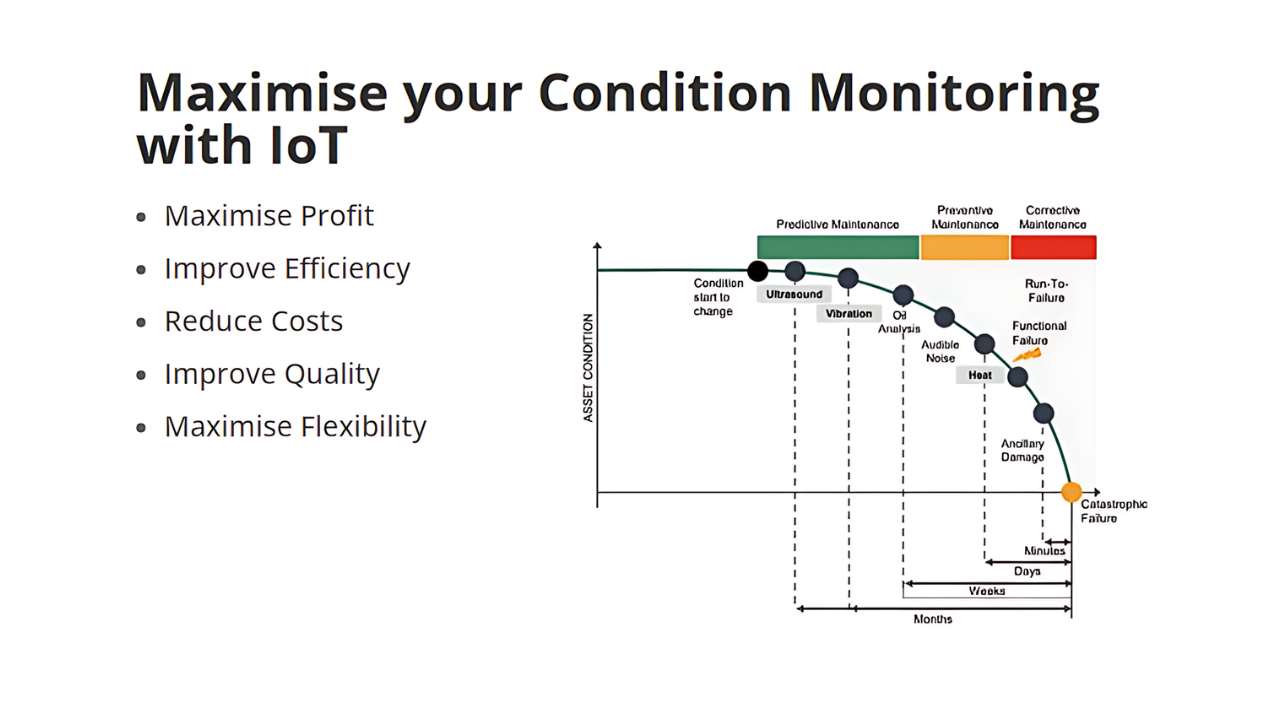
Maintenance
- Remote Service
- Field Technician/ Inspection Efficiency
- Data-Driven Maintenance
- Product Intelligence
Real-time Production Performance Monitoring
- Provides a prescriptive way to capture, contextualize and visualize your Overall Equipment Efficiency (OEE) data with a template that is architected for speed to value, rapid scale and impact
- These insights drive identification of under performing assets and allow new efficiencies to be identified and acted upon
Essential Steps for implementing IoT Condition Monitoring
- Identify the assets that require monitoring
- Identify the known and possible failure modes of those
assets - Identify and install the sensors that will recognize these
failures modes – and an IoT platform for monitoring and
analysing the data - Define baseline limits that will determine when the system
should alert the technicians
5- 20% 2- 10%
Increase in OEE Increase in yield
Gain a real-time, holistic view of your operational performance across your plants, lines and assets
Dashboard overview
- In-Depth Availability Data
- Root Cause Analysis
- Export Raw Data
- Quality & Performance Data
- Automate Data Capture
- Reason Tree Configuration
- Alert Notification
- Key Performance Indicators
IoT based Condition Monitoring Case Study
CHALLENGES
Client had difficulty monitoring pumps that undergo cavitation
intermittently, ultimately causing impeller wear and possible
failure
RESULTS FROM IMPLEMENTING AN IOT PLATFORM
Improved profitability through remote monitoring and predictive
maintenance of complex fluid control systems:
- Avoided a $16 million cavitation problem
- Reduced unplanned maintenance costs and emergency work
orders - Enhanced equipment availability & efficiency
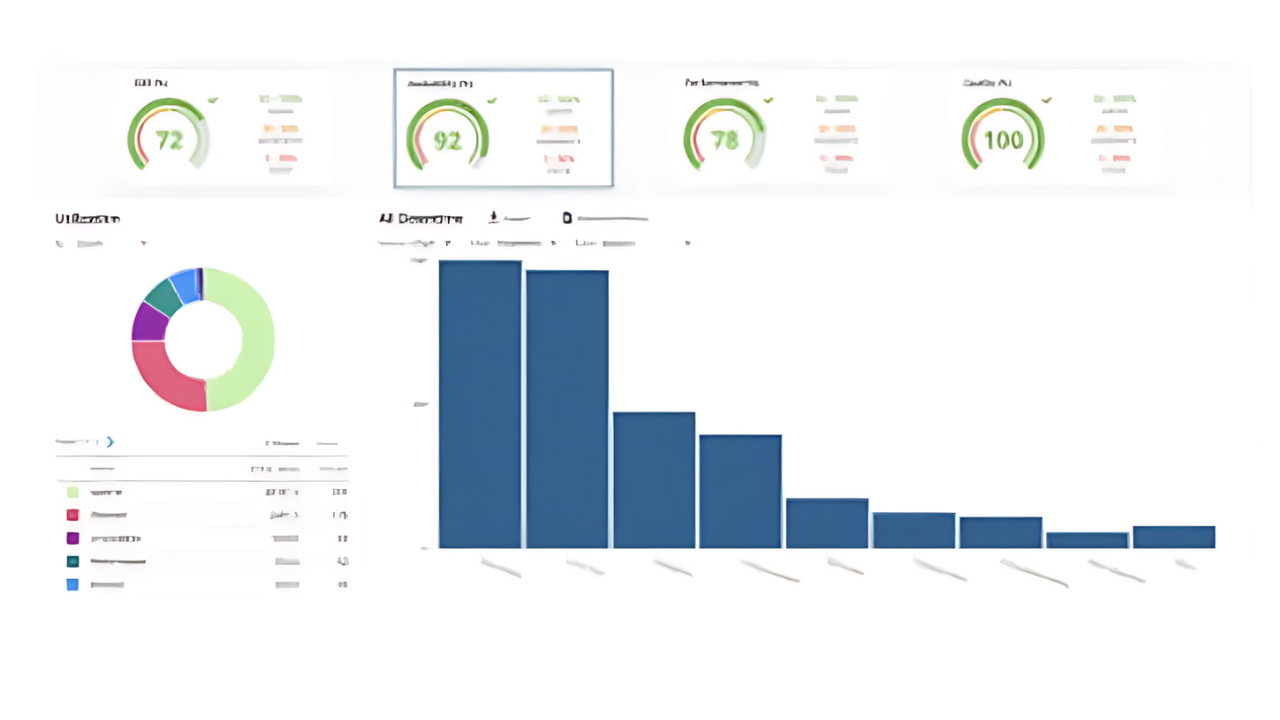
An end- to- end Smart solution for Predictive Maintenance
A complete solution for real time monitoring of industrial equipment
which includes 3 main components:
1. Multi Sensors Device ( tri-axial vibration, ultrasound, temperature)
- Learn & Monitor
- Analyse before transmission
2. Network & cloud server
- Scalable Server Technology
- Secured, encrypted transmission
3. Monitoring Platform
- Visualisations
- Alerts
- Set-up & configuration
What is Digital Transformation ?
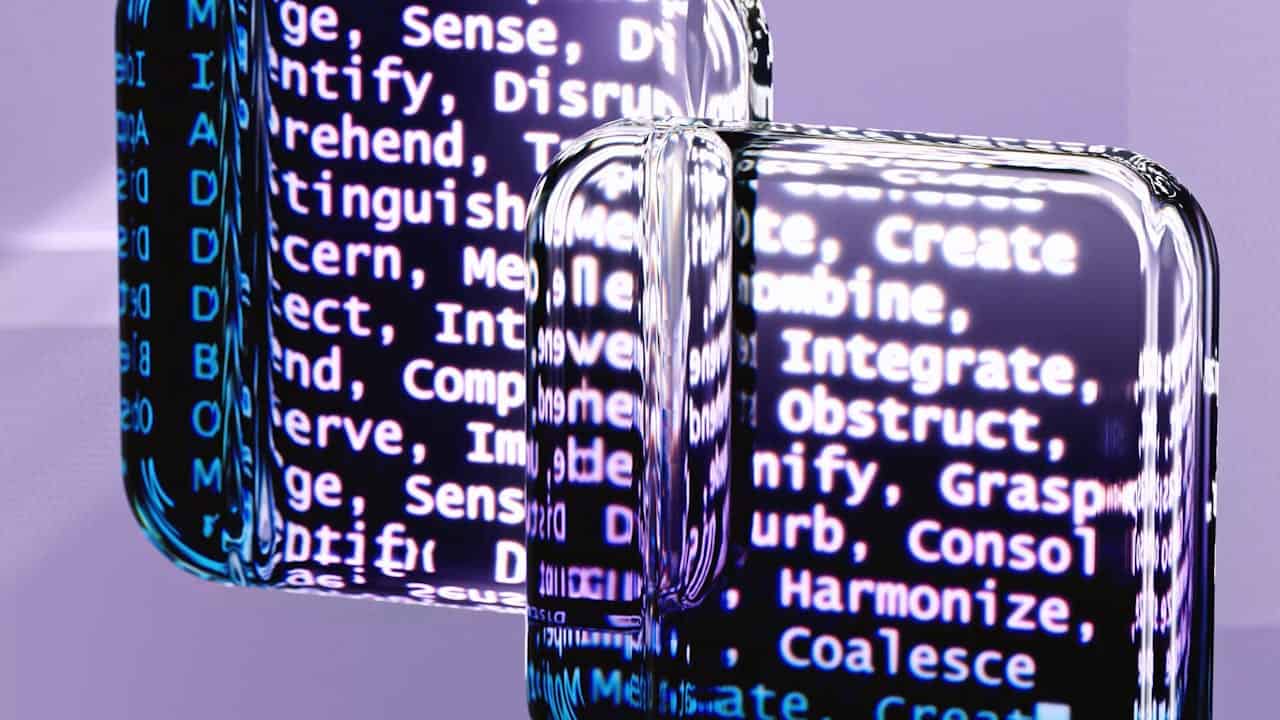
Call For a Quote:
+44(0)7550680067
F.A.Q.
What is digital transformation used for?
Digital transformation is the process of using digital technologies to create new — or modify existing — business processes, culture, and customer experiences to meet changing business and market requirements.
What is the main goal of digital transformation?
Digital transformation is the integration of digital technology into all areas of a business, fundamentally changing how you operate and deliver value to customers.
How is digital transformation changing the world?
Digital transformation helps an organization leverage some of the latest technologies and keep pace with emerging customer demands. It enables organizations to better compete in an economic environment that is constantly changing as technology evolves.