Composite Design and Simulation
We specialize in composite design and composite FEA, providing advanced engineering services for industries requiring high-strength, lightweight materials.
Our expertise includes:
Non-Metallic Materials (NMM) applications in non-metallic piping, non-metallic structures, and engineered plastics.
FRP (Fiberglass Reinforced Plastic) and GRP (Glass Reinforced Plastic) solutions for structural applications.
Composite vessels, composite tanks, and fiberglass tanks for specialized storage and transportation needs.
Finite Element Method Analysis (FEM Analysis) to predict the behavior of composite materials under extreme conditions.
Composite Pressure Vessels designed using advanced simulation techniques.
hat connects the information and processes used across the whole asset lifecycle on one platform, enabling a single version of the truth. This will dissolve the boundaries between functional teams, connecting multiple production locations and streamlining operational management

What is Composite Design & Simulation
Composite Design & Simulation involves engineering structures using layered materials (e.g., carbon fiber, fiberglass) to optimize strength, weight, and performance. Simulation employs advanced software to model stress, thermal behavior, and failure modes, ensuring reliability under real-world conditions. It enables industries like aerospace and automotive to create lightweight, high-durability components cost-effectively.
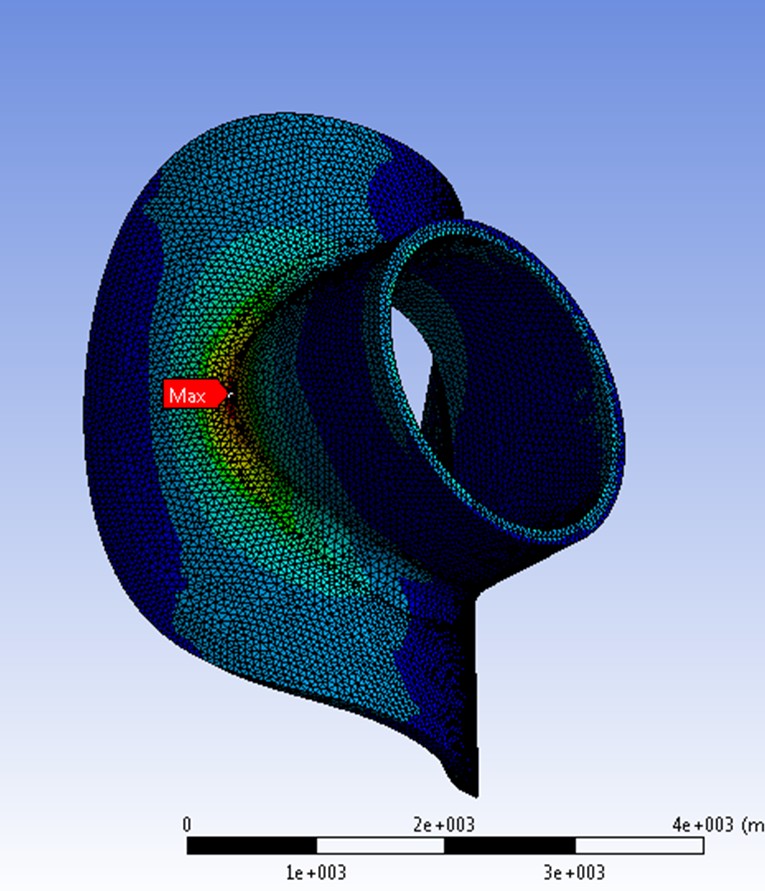
Call For a Quote:
+44(0)7550680067
F.A.Q.
Feel free to ask any questions you might have.
Why Choose Composite Materials Over Traditional Metals?
Composites offer superior strength-to-weight ratios, corrosion resistance, and design flexibility. Simulation validates their performance for industries like aerospace, automotive, and wind energy, reducing prototyping costs and accelerating time-to-market.
Which Industries Use Composite Design & Simulation?
We serve aerospace (aircraft components), automotive (lightweight chassis), marine (durable hulls), renewable energy (wind turbine blades), and sports equipment (high-performance gear).
What Software is Used for Composite Simulation?
Industry-leading tools include ANSYS Mechanical, SolidWorks Plastics, HyperMesh, and LS-DYNA for stress analysis, delamination checks, and failure prediction under extreme conditions.
How Does Simulation Improve Composite Product Reliability?
Simulation identifies weak points, optimizes fiber orientation, and predicts failure modes (e.g., buckling, fatigue). This ensures compliance with ASME BPVC and ISO 527 standards while reducing material waste.