RELIABILITY IMPROVEMENT – RUBBER CHEMICAL PLANT
Industry
Petro Chemical
Service
Petro Chemical
Expertise
Petro Chemical
Background
The process of manufacturing a product consists of a condensation reaction of acetone with aniline in a glass-lined reactor with HCL as catalyst. The HCl is neutralised using caustic soda (NaOH). The condensation reaction is followed by polymerisation to form the product
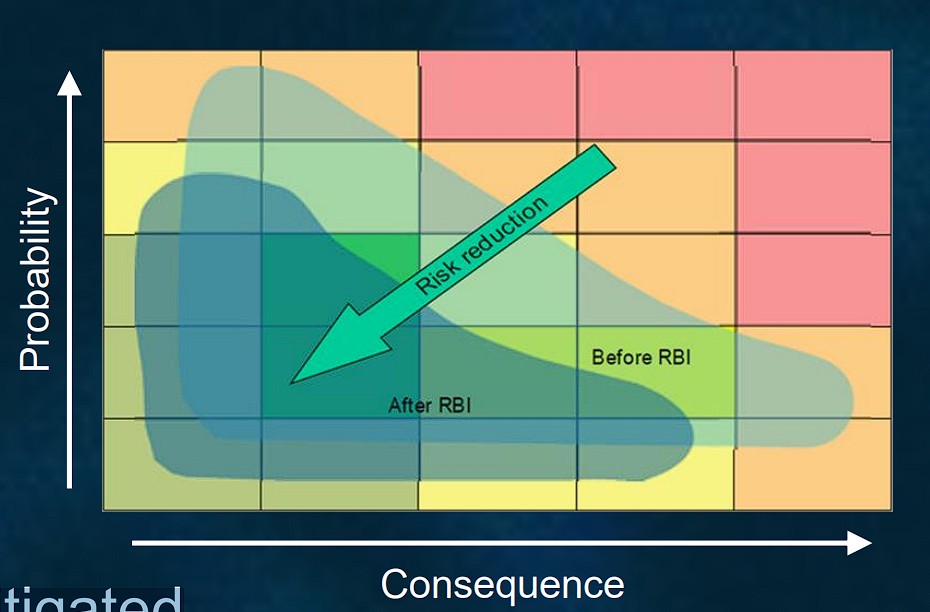
Challenges
- Severe frequent breakdowns of various equipment
- Black swan events (catastrophic failure of H2 reformer tubes and leakage of hazardous liquid from Agitator glands)
- Outcomes
- The RAMS study identified the bad actor’s equipment causing majority of the failures:
- H2 reformer tube was found to be cracked causing catastrophic disruption due to thermal ageing of the reformer tube bellows
- Weld joints were defective – welding process incorrect and the weld joints were not properly stress relieved in the previous repair.
- lubrication, preventive overhauling of the equipment was inadequate
- Corrective actions taken:
- Resolution location-specific issues (vibration/heat etc), Lubrication schedule etc
- A variable frequency Condition monitoring regime (age and criticality focussed)
- Appropriate welding process selected and stress reliving with the replaceable spare reformer tubes and bellows
- Service changeover schedule modified (prevent simultaneous wear-out of redundant equipment)
- A FRACAS programme was deployed to monitor the modified assets and the teething trouble were root analysed and mitigated
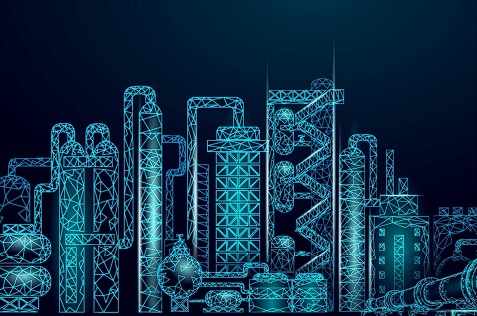