Advanced Engineering Consultancy Services
Cygnas Solutions Ltd offers end-to-end engineering consultancy services, supporting a range of industries, including oil & gas, renewables, aerospace, and manufacturing.
Our services include:
- Engineering Studies & Design for new and existing assets.
- Advanced Engineering Solutions incorporating AI, ML, and Industry 4.0 methodologies.
- Reverse Engineering for legacy equipment and obsolete components.
- Asset Integrity Management using state-of-the-art simulation tools.
- Risk-Based Asset Management optimizing long-term performance and reliability.
- End-to-End Mechanical Design Services from concept to detailed engineering.
Recommended Image: A high-resolution engineering concept illustration displaying multi-industry applications.
For more information, contact Cygnas Solutions Ltd, a leader in advanced engineering solutions and engineering consultancy services, to explore how our expertise in FEA Analysis, pressure vessel design, and finite element analysis services can enhance your project’s performance and reliability.
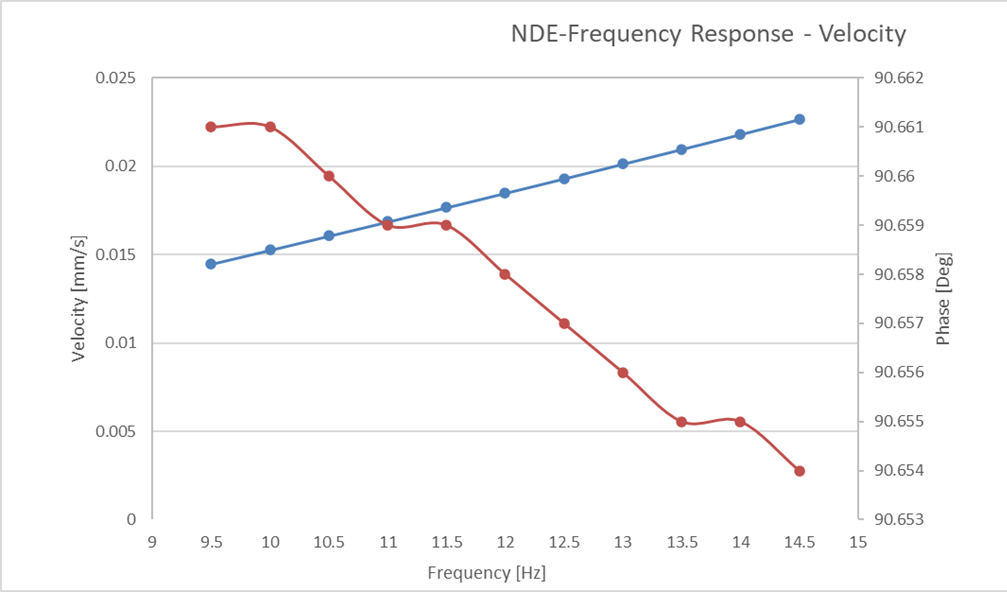
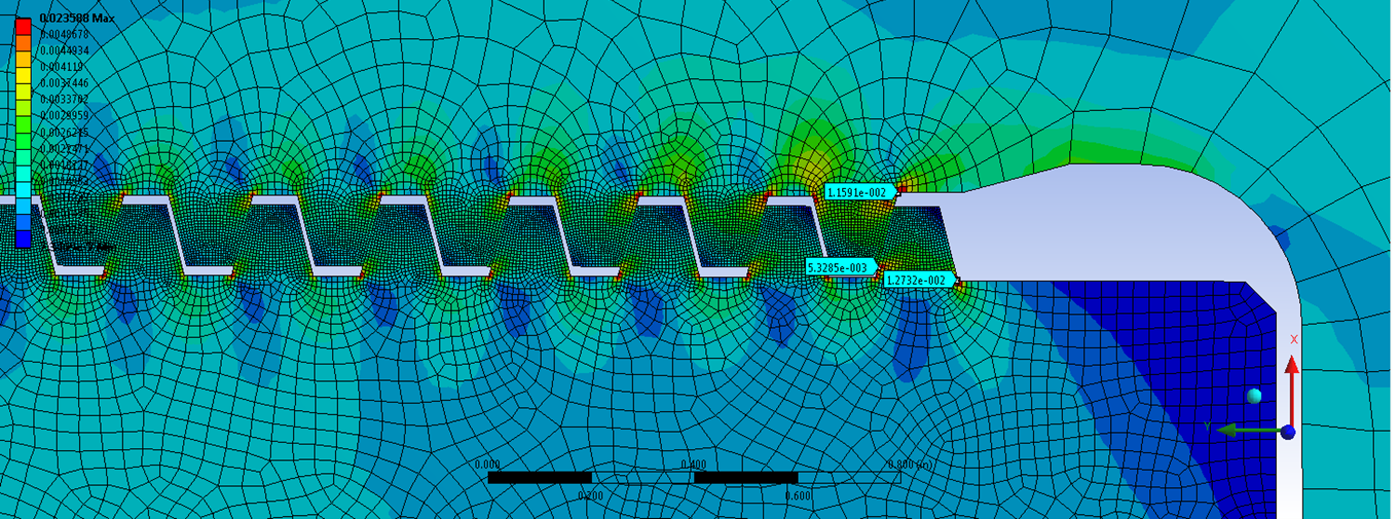
What Are Advanced Engineering Services ?
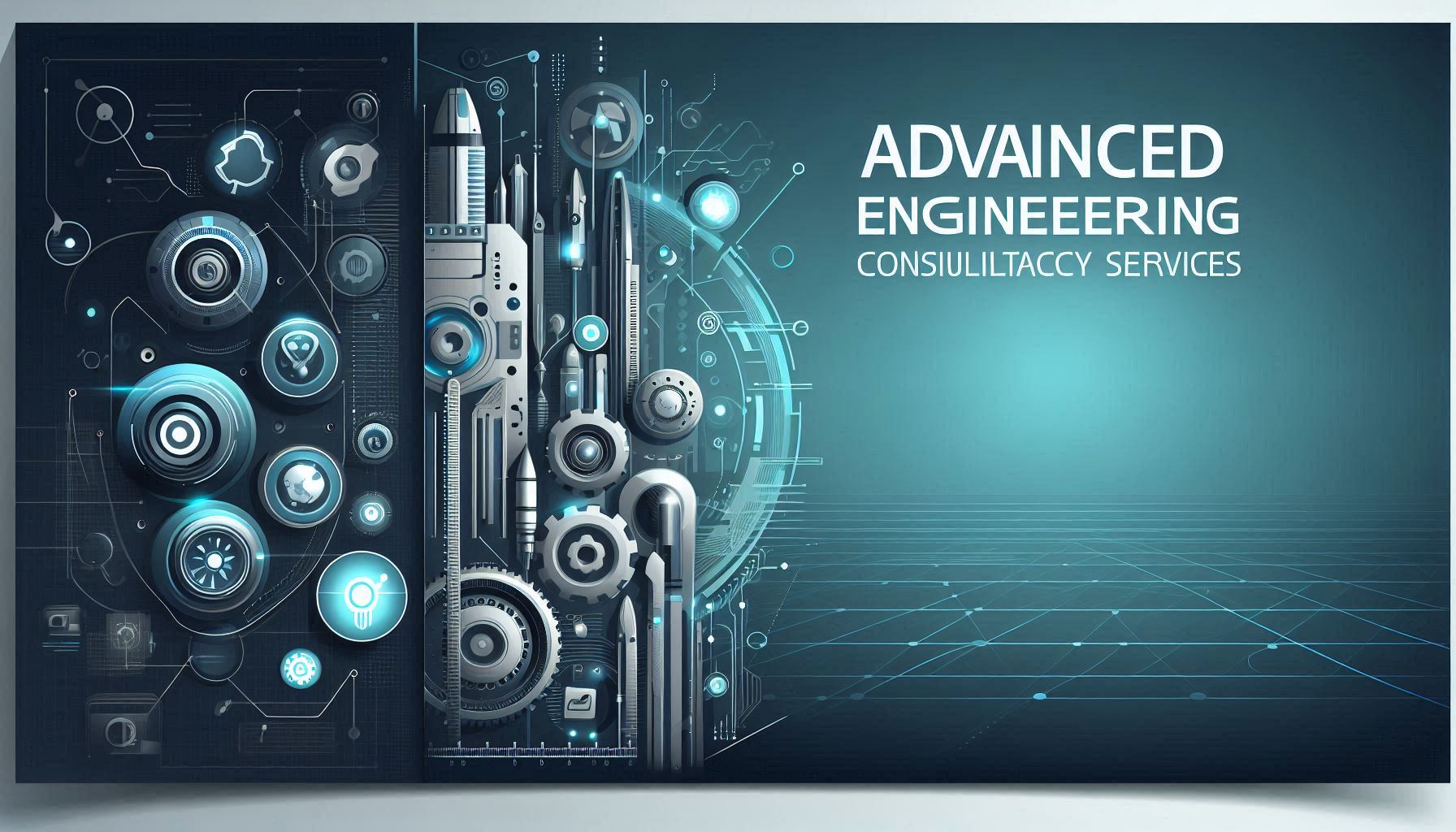
Call For a Quote:
+44(0)7550680067
F.A.Q.
Feel free to ask any questions you might have.
What industries benefit from Advanced Engineering Consultancy Services?
These services cater to aerospace, automotive, energy (oil & gas, renewables), manufacturing, and infrastructure sectors. They address challenges like lightweight design, thermal management, structural integrity, and compliance with ASME, ISO, or API standards.
How do Advanced Engineering Services differ from general consultancy?
They leverage cutting-edge tools like AI-augmented simulations, digital twins, and IoT-enabled monitoring to deliver predictive, data-driven solutions. Unlike general services, they focus on niche technical domains (e.g., composite fatigue analysis, multiphase CFD) and bespoke R&D for innovation-driven industries.
Can these services reduce project costs and timelines?
Yes. By combining FEA/CFD analysis, failure mode prediction, and rapid prototyping, they minimize physical testing, avoid redesigns, and accelerate time-to-market. For example, digital twin integration can cut downtime costs by 30–50% in industrial systems.